墨轲
德国工业4.0专家,德国联邦经济发展和对外贸易协会北京首席代表
近日,在2025全球数字经济大会(GDEC)第五届中国数据要素50人论坛上,德国工业4.0专家,德国联邦经济发展和对外贸易协会北京首席代表、德国菲索玛特(中国)智能制造有限公司执行董事、德国Vivaldi人工智能工业应用公司董事墨轲,以“工业4.0与工业数据价值”为题发表了主题演讲,系统阐述了工业4.0的演进路径与战略转型,工业数据对未来制造业的价值,以下为演讲的主要内容:
在全球制造业加速迈入数字化、绿色化与平台化发展的新阶段,工业数据的战略价值已成为企业竞争力重构的关键变量之一。然而,围绕“工业数据驱动的价值链重塑”这一议题,当前学界与实务界尚存在显著的分析盲区:其一,数据从采集对象到价值资源的转化机制缺乏系统性建模;其二,不同企业与国家间在平台架构、标准体系与组织能力方面存在结构性差异;其三,在国际产业协同背景下,跨国数据互操作与治理机制缺乏经验性验证。
一、工业4.0的演进路径与战略转型
自2011年“工业4.0”在德国汉诺威工业博览会正式提出以来,该术语已从最初的工业战略倡议,演变为涵盖技术、经济与制度多维度的全球制造范式重构框架。尤其是在过去十余年间,其内涵与外延经历了从“智能工厂”向“数字主权”、“数据主导型产业生态”乃至“可持续与韧性导向型系统架构”的深度演进。
在最初的阶段,德国“工业4.0”强调通过嵌入式系统、物联网(IoT)与信息物理系统(CPS)的结合,实现设备层级的高度互联与本地智能。其目标在于构建可自感知、自决策、自优化的“智能工厂”体系。然而,随着技术发展与全球产业格局的演化,这一概念逐渐扩展为对整个价值创造系统的重新理解——数据已从“操作副产品”转变为战略性资产,而工业平台、人工智能、系统韧性等议题也被纳入核心框架。
从战略视角出发,未来的“工业4.0”将不再依赖技术驱动的线性升级模式,而是转向基于“平台化协同—数据智能—系统韧性”三位一体的多极演进路径。
二、工业数据是未来制造的核心资产
在以工业4.0为代表的新一代制造体系中,工业数据已从原有的“工艺附属信息”跃升为决定企业核心竞争力的关键生产要素,其战略地位不亚于传统的资本、原材料与劳动力,被广泛视为制造业数字化、网络化、智能化转型的“基础燃料”。从数据的产生、集成,到其在生产维护、工艺优化、产品设计等环节的系统性利用,构成了智能制造生态中的关键闭环。
工业数据的采集覆盖整个制造生命周期,其来源不仅涉及设备与工艺的运行状态,还涵盖能源消耗、环境变量以及人机交互记录等多个维度。主要数据类型包括:
一是生产数据(Production Data):主要通过制造执行系统(MES)与可编程逻辑控制器(PLC)等系统采集,涵盖工艺参数、工时记录、批次编号等,构成生产过程的时序性主线。
二是设备数据(Equipment Data):通过传感器网络和状态监测系统(Condition Monitoring),捕捉温度、振动、电流、电压等参数,支持健康诊断与寿命预测。
三是质量数据(Quality Data):包括在线检测(如机器视觉、X射线检测、三坐标测量)与离线分析(如金相分析、拉伸测试)等,反映最终产品性能与缺陷信息。
四是能源数据(Energy Data):通过智能仪表采集,如数字电表、气体流量计、热能监测设备等,揭示生产系统的能耗曲线与节能潜力。
然而,这些数据在实际系统中呈现出多源异构、高频波动、语义割裂的特征。不同供应商的设备采集标准差异显著,不同层级系统(如MES与ERP)的接口标准不统一,导致“数据孤岛”与“语义鸿沟”广泛存在。
三、从“智能工厂”走向“数据驱动的价值链协同”
德国制造业的数字化转型最初聚焦于“智能工厂”—通过嵌入式系统与车间级自动化设施提升生产现场的认知、自优化与灵活性。然而,这种“局部智能”模式在面对制造场景的多样化、柔性化与生态协同要求时,逐渐暴露出其边界限制。现代制造不再满足于单点优化,而是寻求跨系统、跨组织、跨地域的全流程价值链协同创新。在这一背景下,“数据驱动的价值链”成为德国先进制造企业的战略重心。
在这一演进过程中,德国领先的制造企业建立起完整的端到端数据闭环机制:数据从设备与生产流程层被精细采集,通过边缘节点预处理后上传至工业云平台,接着集成至平台生态体系,再反馈回供应链与客户服务。Bosch Manufacturing Cloud 与 Siemens Industrial Edge 等平台通过统一的数据接口和算法部署,将冷热链、物流、设计、运营与客户使用环节的数据联通,形成从制造到设计再到服务的动态闭环体系。
如何支撑这一体系落地,一是采用边缘计算技术,如 Bosch 与 German Edge Cloud 联合开发的 ONCITE 边缘云,可在车间局部完成大规模数据并行预处理、实时推理与快速决策,从而规避网络延迟及带宽瓶颈;二是基于工业云平台的生态构建,Bosch Manufacturing Cloud 与 Siemens Edge 等提供了集中算法部署、跨设备协同以及跨工厂可复用组件,使得“规模化智能”成为可能;三是多层级数字孪生系统的引入,使物理生产过程与知识图谱/语义模型融合,赋予制造过程虚拟预演、故障预测与性能优化能力。
总体看来,德国企业正由“工厂数字化”向“价值链数字化”完成跃迁。数据已从生产辅助资源升级为战略基础能力,其管理水平、平台集成与协同运营能力决定了企业在外部市场冲击下的响应速度以及在创新型制造格局中的核心地位。然而,该转型也面临诸多挑战:不同系统间语义不一致,平台封闭性、边缘节点安全性及跨企业数据信任机制尚未成熟,需要中德两国专家交流与合作。
总之,工业数据是制造业竞争力的关键,通过数据分析和人工智能技术的融合应用,可显著提升制造业的效率和质量。中德在智能制造领域的合作潜力广阔,特别是制造业数据集对驱动制造业数智化转型的核心动力尤为重要,中德在制造业数据要素领域的合作前景巨大。
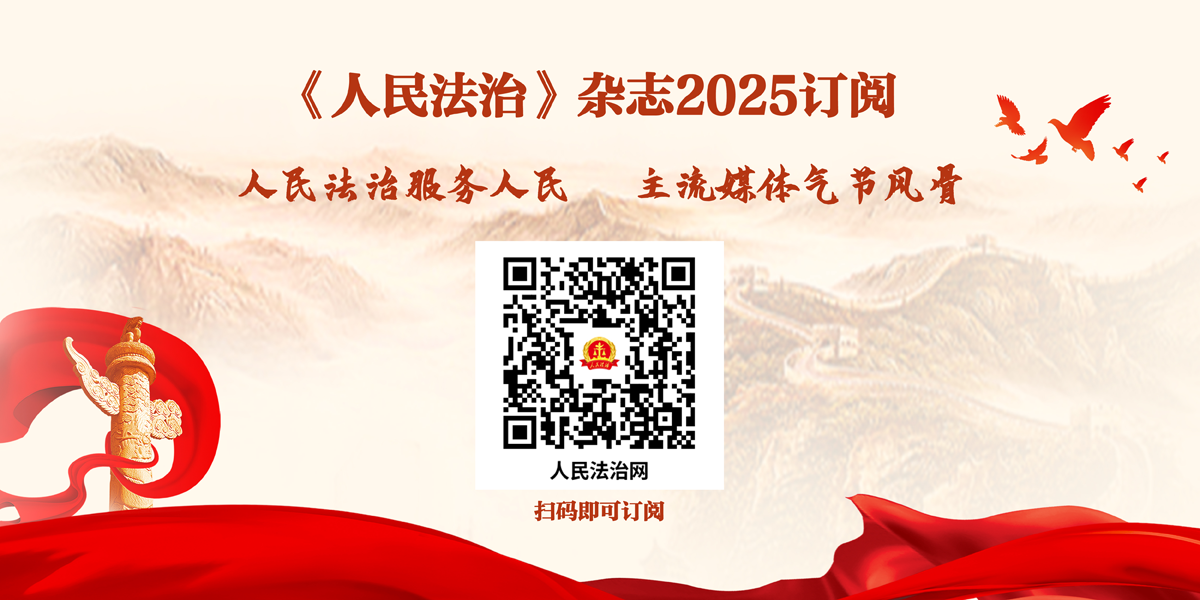